Blog
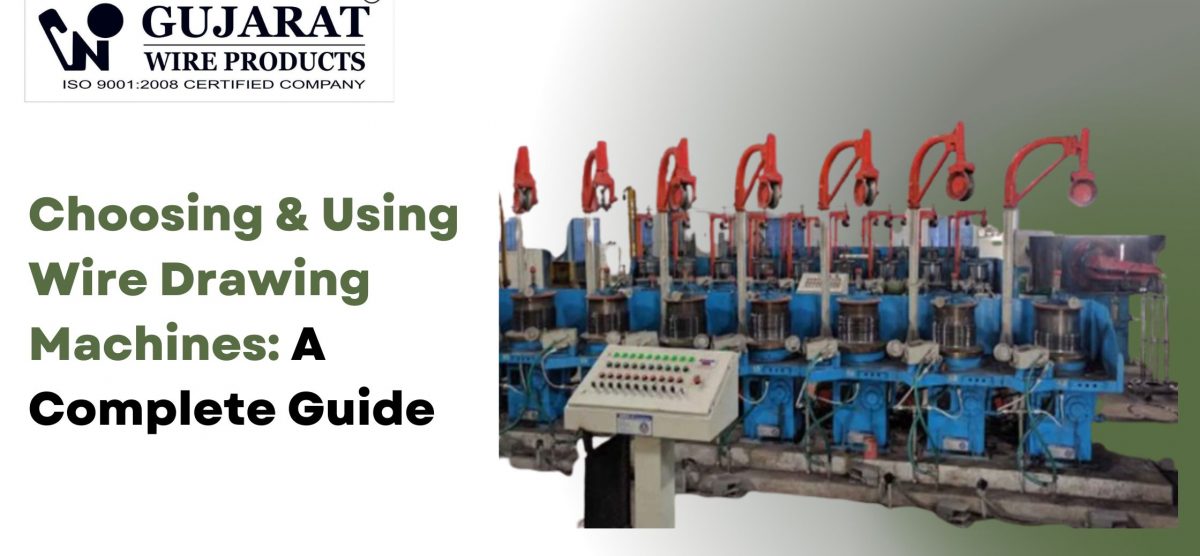
Choosing & Using Wire Drawing Machines: A Complete Guide
Wire drawing machines are the unsung heroes in manufacturing—vital for producing uniform, high-strength wires used in construction, automotive, electronics, and beyond. With the explosion of infrastructure, export opportunities, and new materials in India, choosing and using the right wire drawing machine is crucial for business growth and product excellence. Gujarat Wire Products, as one of the nation’s top suppliers, delivers reliability and technical advantage across the full wire drawing spectrum.
Types of Wire Drawing Machines: Matching the Right Model to Your Production Needs
The wire drawing landscape boasts diverse machine designs, each optimized for different metals, diameters, and output speeds. Understanding machine types ensures you invest in the perfect match for your requirements.
1. Straight Line Wire Drawing Machines
- Ideal for high-speed, large-volume operations.
- Wire moves in a straight, horizontal path—minimizing wire bending and offering superb quality for hard drawing materials (high/medium carbon steel, stainless).
- Minimizes surface defects; supports up to 30 wire draws in one line.
2. Pulley Type Wire Drawing Machines
- Best for flexible medium-volume needs.
- Utilize pulleys to guide wire through dies; ideal for mild steels, copper, and soft alloys.
- Lower operating velocity compared to straight line types but excels in versatility.
3. Water Tank Wire Drawing Machines
- Specialist for fine wires (copper, stainless, etc.).
- Water-cooling throughout the drawing process ensures excellent surface finish and high-speed cooling.
- Favoured in cable manufacturing and fine wire industries.
4. Vertical/Vertical Axis Wire Drawing Machines
- Handles large-diameter bars and wires.
- Gravity-assisted design benefits heavy rods and high-tension applications.
Each type serves unique roles in the cable, fastener, construction steel, and specialty wire industries.
Core Applications: Where Wire Drawing Machines Excel
Wire drawing machines are indispensable for:
- Copper, aluminum, and stainless steel wire for electric cables
- Steel bars and wires for construction rebars and mesh
- Wires for screws, nails, fasteners, and springs
- Fabrication of steel wire ropes, fencing, and specialty mesh
The breadth of application makes them fundamental across industrial and infrastructure sectors.
State-of-the-Art Technologies in Wire Drawing Machines
Frequency Conversion Speed Regulation
Thanks to advances like frequency converters, today’s wire drawing machines deliver:
- Automatic speed adjustment for energy efficiency and process optimization
- Fine control over wire tension and take-up rates
- Reduced mechanical wear and lower unit energy consumption
- Smoother transitions during acceleration, deceleration, and size changes
This translates to higher quality, less waste, and easier operation.
Synchronization and Tension Control
- Synchronous control and advanced PID feedback systems manage multiple drawing heads, keeping wire tension stable and diameter consistent—even at high speeds.
- Tension control at the take-up and pay-off stage ensures perfect winding and packaging, preventing damage and making downstream processing easier.
Modular Equipment & Line Integration
Suppliers like Gujarat Wire Products provide complete lines—including wire pay-off stands, descaling units, straightening and cutting machines, pointing devices, drawing dies, and automated discharging systems—all seamlessly integrated for continuous, high-yield production.
Selecting the Right Wire Drawing Machine: Key Criteria
Making an informed purchase means considering:
- Wire material: High-carbon steel requires robust, wear-resistant machines and dies, while copper or aluminum favor machines optimized for soft metals.
- Output size and volume: High-speed straight line machines for large-scale steel; water tank designs for fine or specialty wires.
- Required surface finish and mechanical properties: Essential for export-quality wire or specialty industrial applications.
- Power requirements and workspace layout: Ensure compatibility with plant infrastructure.
- Automation and integration needs: For scalability and future expansion, choose automation-ready systems.
Example: Choosing Rebar Wire Machines
- Use statistically indeterminate layouts with calculated bar and steel combinations for crack resistance and economy.
- Grade-3 steel and combinations like 30+3 grade yield strength and flexibility for demanding standards.
Step-by-Step: The Wire Drawing Process
- Raw Wire/Bar Preparation
- Decarburization, descaling, or surface treatment directly affects end-product quality.
- Pointing, Feeding, and Pay-Off
- A wire end is “pointed” for easy die insertion; pay-off system ensures smooth feeding.
- Drawing Sequence
- The wire passes through decreasing die sizes, elongating and thinning with each stage.
- Cooling (air/water) systems dissipate process heat.
- Tension and Speed Regulation
- Frequency inverters or dual-frequency systems manage drum and pay-off speeds.
- Take-Up and Winding
- Advanced winders use synchronous and tension control for neat, damage-free coils.
- Finishing
- Inline or post-process annealing, straightening, and cutting dependent on wire end-use.
Essential Maintenance for Wire Drawing Machines
Longevity and top performance depend on disciplined maintenance:
- Keep dies and guides clean to prevent wire scoring.
- Lubricate moving parts to minimize wear, especially in high-speed lines.
- Monitor for alignment and tension issues—regularly check sensors, belts, and couplings.
- Replace worn drawing dies promptly to avoid diameter drift and surface defects.
- Upgrade software and control systems as needed for optimal synchrony and efficiency.
Optimizing Production with Gujarat Wire Products
Comprehensive Solutions
- Full wire drawing system supply: point to finished coil or straight length
- Customization for specific wire grades, diameters, and production scales
- After-sales support: installation, commissioning, training, and technical troubleshooting
Industry Leadership
- Decades serving rebar, cable, fastener, and specialty wire factories
- In-house R&D and manufacturing for machine bodies, electrical systems, and automation
- Continuous upgrades for frequency conversion, digital controls, and integrated line automation
Frequently Asked Questions
Q: Can Gujarat Wire Products customize wire drawing lines?
A: Yes—designs cover copper, steel, aluminum, fine, and large-diameter wire systems.
Q: How important is frequency conversion in new machines?
A: Critical for energy efficiency, adjustable speed, reduced downtime, and competitive operating costs.
Q: What after-support is provided?
A: Full service includes installation, operator training, spares, and ongoing technical advice.
Q: What projects are these machines best suited for?
A: Everything from basic construction rods and mesh, to fine-cable, fasteners, and complex multi-die operations.
Conclusion: Secure Your Competitive Edge with Gujarat Wire Products
Choosing and using the right wire drawing machine is foundational to quality, cost management, and production agility in today’s metal industry. With advanced technology, comprehensive product lines, and proven support, Gujarat Wire Products is your partner in building a resilient, future-proof wire manufacturing operation.
Optimize your wire drawing—choose Gujarat Wire Products for reliability, innovation, and unrivaled value.