Blog
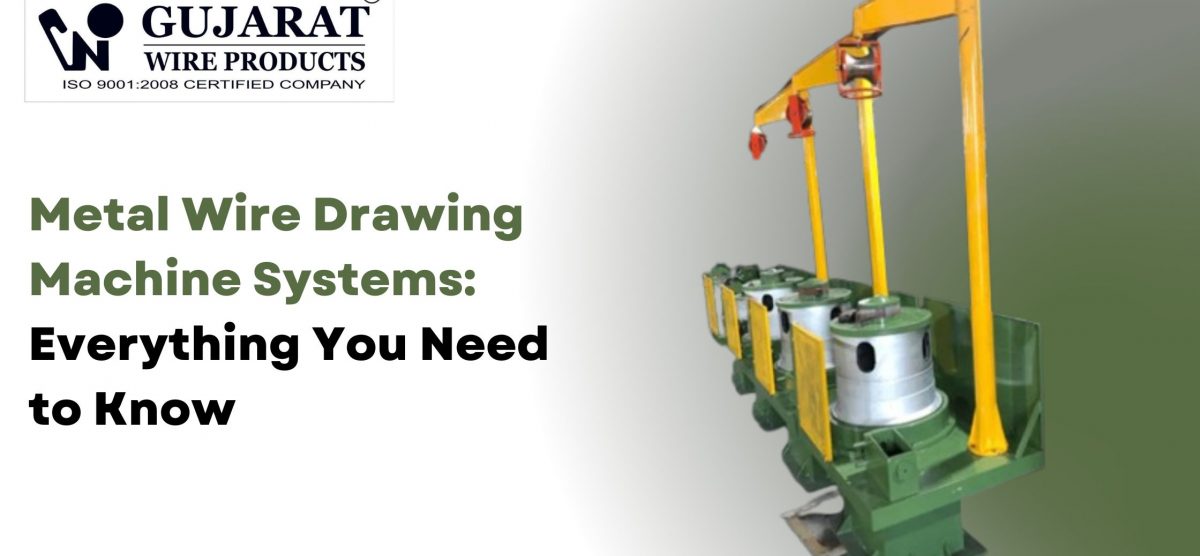
Metal Wire Drawing Machine Systems: Everything You Need to Know
In the world of industrial metal processing, wire drawing machines play a crucial—but often underappreciated—role. Whether manufacturing fasteners, cables, fencing, springs, or structural reinforcements, quality begins with the wire. From construction and automotive, to electronics, textiles, and white goods, countless sectors depend on wires whose performance, strength, and finish are determined in the wire drawing workshop. Gujarat Wire Products, at the forefront of India’s machine tool sector, brings you an in-depth look at everything that defines today’s advanced metal wire drawing machine systems.
What Is a Metal Wire Drawing Machine?
A metal wire drawing machine reduces the diameter of thick wire rods into fine, precise wires by pulling them through a series of hardened dies. This process is not just about changing dimension—it’s about improving the wire’s roundness, straightness, internal structure, and surface quality, transforming rough wire rods into material perfectly suited for manufacturing.
Key roles of wire drawing machines:
- Achieve specific diameters and tolerances
- Enhance surface brightness and smoothness
- Improve mechanical properties via work hardening
- Enable mass production for a variety of wire-based products
The Core Processes in a Wire Drawing Machine Line
A well-designed wire drawing line involves several coordinated steps, each impacting the quality of the final wire. Here’s how a typical system operates from start to finish:
1. Wire Pay-off
Raw wire coils or rods are placed on pay-off stands that smoothly feed the wire into the production line. Systems vary from manual to fully automated, depending on scale and speed.
2. Surface Treatment
Surface cleanliness is paramount. Rust, scale, and grime are removed using mechanical descalers, pickling, or phosphating, ensuring smooth passage through dies and reducing die wear. This step also improves surface finish and performance of the drawn wire.
3. Wire Pointing
A pointing machine is used to reduce the wire end, allowing it to enter the smallest die smoothly. This small—but critical—step avoids jamming and equipment damage.
4. Drawing Through Dies
The heart of the system: the wire passes through a series of dies (usually made of tungsten carbide or diamond), each progressively reducing diameter. The number of drawing passes and die materials are chosen based on metal type, desired final size, and quality requirements.
5. Cooling & Lubrication
Heat generated by friction is controlled with coolant or lubricant, extending tool life and ensuring wire quality. Proper lubrication also prevents galling and micro-cracks on the final wire surface.
6. Inline Quality Monitoring
High-end systems integrate sensors, laser gauges, and non-contact measuring devices for real-time monitoring of wire diameter, surface, and defects—enabling immediate adjustments.
7. Wire Take-up
Finished wires are wound onto spools, coils, or reels, ready for downstream use or packaging. Automated take-up systems boost efficiency and reduce labor costs.
Types of Metal Wire Drawing Machines
1. Pulley (Drum) Type Wire Drawing Machine
- Versatile, suitable for medium- to large-diameter wires
- Uses capstans/drums for controlled speed and tension
- Common in construction wire, fencing, and general applications
2. Water Tank Wire Drawing Machine
- Designed for small-diameter wires (like welding wire)
- Immersed in water for continuous cooling/lubrication
- Popular in fine wire and stainless steel applications
3. Vertical Wire Drawing Machine
- For large diameter or heavy wires (e.g., prestressed steel)
- Vertical axis design prevents bending and reduces space requirement
4. Straight-Line Drawing Machine
- Each die and capstan is in a linear arrangement
- Consistent wire tension and speed; easy die replacement
- Preferred for high-precision, high-speed requirements
5. Fine Wire Drawing Machine
- For ultra-fine wires (down to sub-millimeter diameters)
- Uses special dies and precision lubrication/cooling
Applications Across Industries
Wire drawing machines are indispensable in:
- Manufacturing (fasteners, screws, nails, bolts, wire ropes)
- Cables and Conductors (electrical, telecommunication)
- Automotive components (springs, clips)
- Construction (reinforcing meshes, fencing)
- Consumer goods (music strings, zippers, jewelry)
- Petrochemicals and specialty alloys
Critical Factors in Choosing a Wire Drawing Machine System
Factor | Why It Matters |
Material type | Determines die material, cooling, and process |
Wire diameter range | Dictates number of drawing passes and machine size |
Desired output rate | Influences automation, take-up system, drive power |
Finished wire quality | Impacts inline monitoring and lubrication needs |
Space and factory layout | Impacts vertical vs. horizontal machine choice |
Budget and support | Ensures value for money and ongoing productivity |
Technological Innovations in Today’s Systems
High-Efficiency Drives
Modern systems use variable frequency drives (VFDs) or servo motors for ultra-precise speed and torque control—reducing energy use and improving safety.
Advanced Die Materials
Tungsten carbide and polycrystalline diamond dies extend tool life and enhance surface quality, especially in high-speed or high-volume lines.
Intelligent Lubrication
Closed-loop lubrication with filtration units boost tool life and environmental safety while maintaining optimum wire quality.
Automation & Digital Monitoring
PLC controls, touchscreens, digital sensors, and remote diagnostics enable real-time adjustments and predictive maintenance—maximizing uptime.
Wire Drawing Machine Maintenance Best Practices
- Clean dies and wire guides daily to prevent build-up and ensure smooth operation.
- Monitor for abnormal noise or vibration, which can predict wear or misalignment.
- Maintain coolant and lubricant levels; replace filters as per manufacturer guidance.
- Keep sensors and gauges calibrated for consistent product quality.
- Stock critical spares (dies, bearings, seals) to minimize downtime.
The Environmental Edge: Greener Operations
- Energy-efficient drives and motors reduce electricity usage.
- Clean lubrication systems and capture of drawing shavings lower waste.
- Water recycling and closed cooling circuits limit environmental footprint.
- Dust extraction and soundproofing protect workers and workspace.
Gujarat Wire Products: Delivering Value Across the Production Chain
What sets Gujarat Wire Products apart?
- Decades of wire machinery engineering and manufacturing expertise
- A complete lineup: From rod breakdown to fine wire drawing, including all auxiliary machines (pay-off, pointing, welders, take-up)
- Custom system design to fit your layout, material, and capacity needs
- Full after-sales support: Installation, commissioning, operator training, and fast spares
- Strict quality assurance: Each machine undergoes rigorous checks and field testing
Frequently Asked Questions (FAQs)
Q1: Which materials can your machines process?
A: Mild steel, high-carbon steel, stainless steel, copper, aluminum, and specialty alloys—with optimized dies and system configuration for each.
Q2: Can these machines be integrated into Industry 4.0/automated environments?
A: Absolutely—Gujarat Wire Products offers PLC integration, remote diagnostics, and inline data monitoring to suit smart factories.
Q3: What about installation and operator training?
A: Every system comes with on-site installation and hands-on personnel training, plus manuals and troubleshooting guides.
Q4: What is the typical lifespan of your wire drawing machines?
A: With regular maintenance, systems often deliver 10–15 years of reliable service, sometimes more.
Case Study Highlight
A major fastener manufacturer increased production yield by 30% and slashed defect rates after upgrading to a fully-automated, straight-line drawing system by Gujarat Wire Products—demonstrating not just process improvement, but real-world profit.
Conclusion: The Foundation for High-Quality Manufacturing
Precision wire production is the first step to world-class fasteners, cables, and components. Metal wire drawing machine systems by Gujarat Wire Products deliver unmatched reliability, efficiency, and versatility—ensuring you can meet the demands of today and the innovations of tomorrow.
Upgrade your manufacturing with Gujarat Wire Products. For robust, future-ready wire drawing solutions—trust the experts in Indian metal processing machinery.