Blog
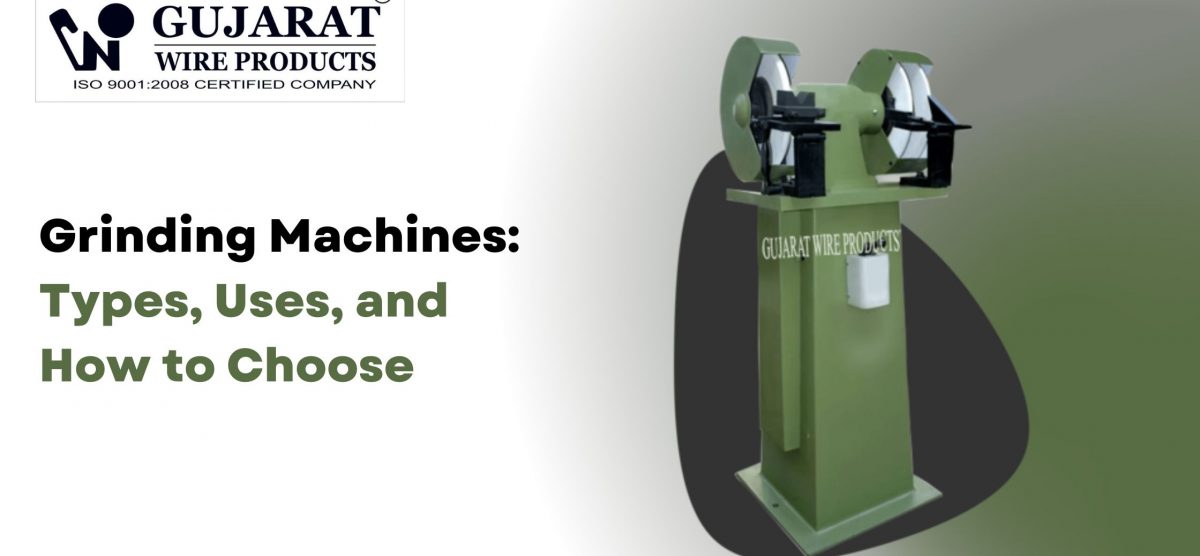
Grinding Machines: Types, Uses, and How to Choose
Grinding machines are the backbone of precision engineering across industries worldwide. From manufacturing automobile parts to crafting delicate surgical equipment, their versatility and accuracy make them indispensable. With the global grinding machine market expected to reach nearly $8.2 billion by 2025, these tools are fueling growth and innovation in sectors like automotive, aerospace, construction, and metalworking.
What Is a Grinding Machine?
A grinding machine is a power-driven tool equipped with an abrasive wheel or belt, designed to remove small amounts of material for shaping, finishing, or sharpening a surface. Known for delivering high accuracy and surface finish, grinding machines are crucial where exact tolerances and smooth finishes are needed (for metals, ceramics, glass, and composites).
Main Types of Grinding Machines
Grinding Machine Type | Key Function/Use | Common Materials |
Bench Grinder | Sharpening tools, shaping | Metal, steel |
Belt Grinder | Deburring, finishing | Metals, plastics |
Surface Grinder | Flat surface finish | Metals, ceramics |
Cylindrical Grinder | Grinding cylindrical work | Shafts, rollers |
Centerless Grinder | Mass production grinding | Pins, rods, tubes |
Tool and Cutter Grinder | Sharpening cutting tools | Drills, milling cutters |
Internal/Bore Grinder | Boring holes & internal faces | Gears, engine parts |
Gear Grinder | Producing precision gears | Steel, alloy gears |
Jig Grinder | Complex shapes, fine finishes | Dies, jigs |
Die Grinder | Detail work, tight spaces | Metals, composites |
Pedestal Grinder | High-power shaping & cleaning | Heavy-duty steel |
Flexible Shaft Grinder | Large workpieces, mobility | Castings, welds |
Portable Grinder | On-site/off-site operation | Welds, construction |
Detailed Overview of Common Grinding Machines
1. Bench Grinding Machine
Fixed on workbenches, these include dual wheels (coarse and fine) for sharpening, deburring, and tool shaping. Widely used in workshops due to their accessibility and versatility.
2. Belt Grinding Machine
Employs abrasive belts for rapid material removal and fine surface finishing. Popular in metal fabrication for smoothing edges and deburring, and also useful for plastics and composite materials.
3. Surface Grinding Machine
Ideal for achieving highly flat surfaces and tight tolerances. Common in tool manufacturing, automotive parts, and precision engineering.
4. Cylindrical Grinding Machine
Used to grind the external and internal surfaces of cylindrical items like shafts, rods, and roll components, ideal for both small- and large-scale production.
5. Centerless Grinding Machine
Eliminates the need for mounting workpieces on centers, making it ideal for high-volume, consistent production (e.g., pins, rods).
6. Tool and Cutter Grinder
Specifically made for sharpening milling cutters, reamers, taps, and other cutting tools, supporting manufacturing lines with continuous tool-maintenance needs.
7. Internal/Bore Grinding Machine
Specialized for grinding internal diameters. Achieves high-precision finishes for gears, bushings, and engine parts.
8. Gear and Jig Grinders
Gear grinders ensure accurate teeth profiles on gears; jig grinders deliver complex finishes and tight tolerances in dies and intricate components.
9. Die Grinder & Flexible Shaft Grinder
Die grinders allow handheld precision for detailed work in tight or awkward spaces, while flexible shaft grinders suit large castings and weldments.
10. Pedestal & Portable Grinders
Pedestal grinders mount on robust stands for heavy-duty work; portable grinders allow on-the-go finishing and repair jobs.
Factors Influencing Choice of a Grinding Machine
1. Material Type
- Harder materials need specialized abrasives and machines (e.g., carbide tools require diamond wheels).
- For ferrous metals, use aluminum oxide; for non-ferrous, use silicon carbide or CBN.
2. Surface Finish & Tolerance
- Applications needing micron-level precision (engineering, tooling) demand surface and precision grinders.
3. Shape and Size of Workpiece
- Large, awkward shapes may need flexible shaft or swing frame grinders.
- Small, precise jobs suit bench, die, or tool grinders.
4. Production Volume
- Centerless and cylindrical grinders excel in mass production environments.
- Bench, belt, and tool grinders are ideal for smaller runs or maintenance.
5. Speed and Power
- High-speed jobs or deep material removal require robust, high-powered machines.
- Adjustable speed features allow flexibility based on material and application.
6. Safety Features
- Always ensure machines comply with industry safety standards to mitigate risks.
7. Automation and Control
- Modern CNC grinders and automated options offer improved productivity, flexibility, and accuracy.
8. Budget and Cost of Ownership
- Factor in initial price, power consumption, maintenance, and consumables when making a purchase.
Major Industrial Uses of Grinding Machines
- Metalworking: Cutting tool sharpening, component shaping, and surface finishing.
- Automotive: Engine part manufacturing, crankshafts, and transmission gears.
- Aerospace: High-tolerance finishing of turbine blades and structural elements.
- Construction: Preparing flat surfaces, smoothing welds.
- Medical Devices: Creating or refining surgical tools and implants.
- Manufacturing: Continuous tool and die making, mold finishing, and parts refurbishing.
Market Trends and Industry Outlook
- Market Growth: Global grinding machine industry value will climb from $7.58 billion in 2024 to an estimated $8.18 billion in 2025, continuing a trend toward automation, precision, and efficiency.
- Technological Advancements: Digitization, robotics, and Industry 4.0 integration are redefining the sector with enhanced reliability and predictive maintenance.
- Sustainability: Demand is rising for energy-efficient models and sustainable production.
Maintenance Tips to Maximize Machine Life
- Ensure regular dressing of grinding wheels for consistent performance.
- Frequently check alignment, lubrication, and inspect safety shields.
- Replace worn components and belts immediately to prevent secondary failures.
- Calibrate controls and automation systems periodically.
Conclusion
Grinding machines are powerful, diverse, and crucial across modern industries. Choosing the right one requires understanding your application, tolerances, materials, production volume, and budget. With technological advances and market growth on the horizon, investing in the appropriate grinding machinery—supported by expert suppliers like Gujarat Wire Products—is key to achieving world-class results in manufacturing.
For more details on the right machine for your application, consult with Gujarat Wire Products, your partner for reliability, innovation, and support in the world of grinding solutions.