Blog
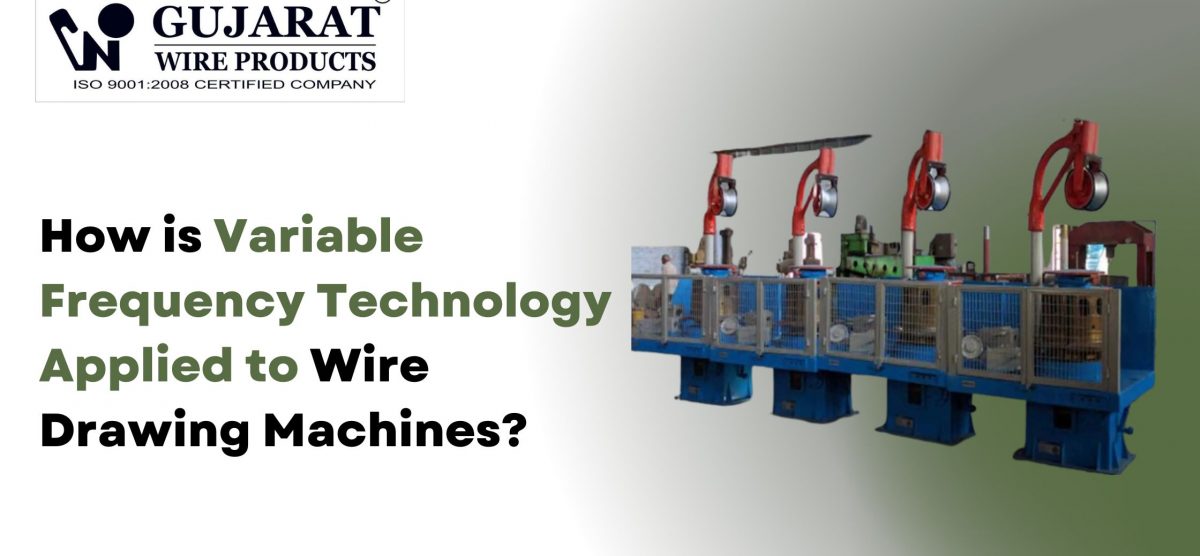
How is Variable Frequency Technology Applied to Wire Drawing Machines?
The wire drawing industry, vital to sectors such as construction, electrical, and manufacturing, has witnessed a technological leap with the adoption of variable frequency drive (VFD) technology. This advancement significantly boosts precision, production speed, energy efficiency, and wire quality. Gujarat Wire Products integrates this technology into its wire drawing machines, redefining performance standards for modern manufacturing.
Understanding Variable Frequency Technology
Variable Frequency Drives (VFDs), also known as inverters, control the speed and torque of AC motors by adjusting the frequency and voltage delivered. In wire drawing, VFDs manage the speed of multiple drawing and winding motors, creating constant tension and precise dimensioning throughout the process.
Key Benefits
- Enhanced energy savings
- Real-time speed and tension control
- Reduced mechanical wear
- Superior product consistency
- Lower maintenance costs
Types of Wire Drawing Machines and Variable Frequency Application
Wire drawing machines include straight, tank, and inverted designs, handling wire diameters from macro to micro levels. Each type benefits from VFD integration for both drawing and winding stages.
Machine Type | Application | VFD Role |
Straight Line | High-speed | Multi-speed control across drawing heads |
Tank Drawing | Fine wires | Smooth transition between stages |
Inverted | Heavy gauge | Real-time torque and tension management |
Why Variable Frequency Technology Outperforms Traditional Systems?
Traditional wire drawing relied on fixed-speed motors and mechanical control, often facing issues like:
- Wire breakage during speed changes
- High maintenance due to mechanical stress
- Inconsistent wire tension causing wastage
With VFDs, these limitations are addressed by delivering stable, adaptable control, even during operation start/stop and diameter transitions.
The Role of PID Controllers in Wire Drawing Machines
A central aspect of variable frequency technology in wire drawing is the use of PID (Proportional–Integral–Derivative) control algorithms. These feedback-based systems monitor and adjust wire tension, speed, and consistency automatically:
How PID Controllers Work
- Detect discrepancies (via sensors) in tension or diameter
- Compensate instantly by adjusting motor speeds in real time
- Maintain optimal wire flow across all drawing heads
This method enables seamless compensation for die wear, motor variations, and process anomalies, dramatically reducing downtime and wastage.
Automation and Intelligence: VFDs Integrate Advanced Control
Gujarat Wire Products leverages advanced VFDs that unify the following functions:
- Integrated Tension Control Algorithms: Maintain constant tension, eliminating manual tuning.
- Multiple Drawing Heads Coordination: Precise, proportional control between stages.
- Emergency Response: Automatic synchronization, defect detection, and rapid response to wire breaks or abnormalities.
- Touchscreen and Remote Access: Allowing parameter setup, monitoring, and troubleshooting via user-friendly interfaces.
Direct Benefits
- No need for external PID controllers: Reduces complexity and cost.
- Built-in protection: Quick alarms and emergency stops prevent accidents and product loss.
- Parameter storage: Quick setup for multiple production runs.
Step-by-Step: How Variable Frequency Drives Optimize Wire Drawing
- Setup and Initialization:
- Operator inputs target wire diameter, material, and speed on the HMI panel.
- VFD parameters are selected or uploaded for the required batch.
- Wire Feeding and Start-up:
- VFDs ensure ultra-low frequency torque for smooth thread start with no sudden jerks or breakage.
- All drawing heads synchronize for proportional flow matching.
- Continuous Operation:
- Real-time sensor data adjusts each stage speed dynamically.
- PID algorithms respond to tension deviations, wear, and external disruptions.
- Dynamic Adjustments:
- Seamless compensation for die changes, motor fluctuations, and wire diameter variation.
- Operators can remotely monitor and tweak parameters, minimizing downtime.
- Smart Shutdown:
- Ramp-down control avoids breakage, maintains synchronization during stop.
- Automated alarms trigger if irregularities or emergencies are detected.
Advanced Features in Modern Wire Drawing VFDs
- Multi-stage programmable control for diverse wire thickness processing
- Automatic roll diameter calculation for precision winding
- Adaptive tension taper control for packaging uniformity
- Predictive maintenance: Alerts for die/tool wear and process issues
- Remote diagnostics and troubleshooting
Comparing VFD Systems: Key Performance Indicators
Feature | Traditional Control | Advanced VFD Control |
Start/Stop Response | Slow, high risk | Smooth, jerk-free |
Tension Consistency | Variable | Constant, precise |
Maintenance Needs | High | Low |
Parameter Adjustability | Manual, limited | Digital, programmable, remote |
Energy Consumption | High | Reduced by up to 20–30% |
Wire Quality and Waste | Inconsistent | Significantly improved |
Real-world Results & Industry Applications
Gujarat Wire Products’ VFD-driven wire drawing lines are widely used for:
- Steel wire for construction and fasteners
- Copper and aluminum wires for electrical applications
- Stainless steel wire for mesh, medical, and specialty uses
Clients report reductions in wire breakage, improved finished surface quality, minimized scrap, and enhanced productivity.
Maintenance and Best Practices
- Maintain calibration of sensors and feedback loops for accurate PID response
- Regularly update firmware and parameter sets
- Train operators on digital adjustment and alarm response
- Monitor for unusual sounds, vibrations, or heat increases
Future Trends: Smart Automation and Energy Efficiency
- Industry 4.0 Integration: Real-time analytics and remote cloud monitoring will soon make VFD-controlled wire drawing even smarter.
- Eco-friendly Production: Expect wider adoption of regenerative drives and low-energy VFDs to further cut both costs and environmental footprint.
Conclusion: Optimizing Wire Drawing with Gujarat Wire Products
Adopting variable frequency technology in wire drawing machines is no longer an upgrade—it’s a necessity for manufacturers seeking higher yields, stable quality, and operational efficiency. Gujarat Wire Products stands at the forefront, delivering machines engineered for stability, precision, and intelligent automation. Whether you handle large-scale or specialty wire production, integrating VFD systems unlocks new levels of productivity and consistency for your business.