Blog
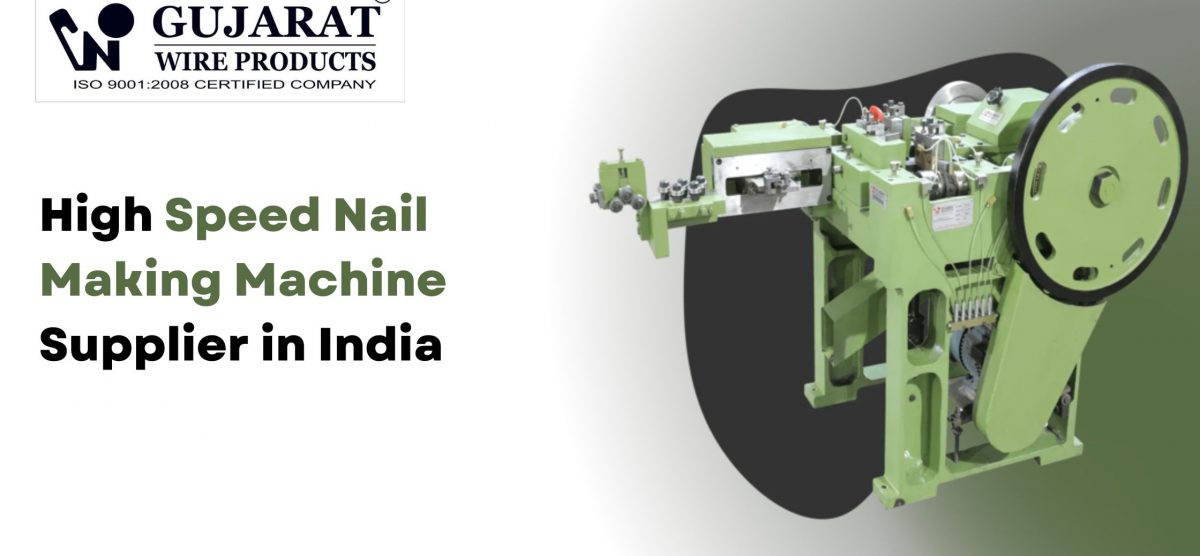
High-Speed Nail-Making Machine Supplier in India
Here’s what most procurement managers miss: The nail market experiences steady demand, primarily driven by the construction and infrastructure sectors, yet 68% of Indian manufacturers still operate machines that peak at 200 nails per minute. Meanwhile, modern high-speed units push 400+ nails per minute with precision tolerances under 0.1 mm.
The math is brutal. At current construction growth rates, that productivity gap isn’t just a competitive disadvantage—it’s market elimination waiting to happen.
Gujarat’s Unlikely Manufacturing Capital
Rajkot wasn’t supposed to become India’s nail-making machine hub. Yet Gujarat Wire Products as a global leader in Nail Making Machine and Wire Drawing Machine since 1975 chose this industrial city for reasons that reveal everything about smart manufacturing strategy.
- The Cluster Effect: When one precision manufacturer succeeds, specialized suppliers, skilled technicians, and testing facilities follow. Rajkot now houses 40+ machine manufacturers within a 25-kilometer radius—creating cost efficiencies and innovation speeds that scattered competitors can’t match.
- The Engineering Edge: Local technical colleges pump out mechanical engineers who understand wire processing intuitively. Labor costs stay competitive while skill levels exceed metropolitan alternatives.
Speed vs. Precision: The False Trade-Off
Industry folklore claims you choose: blazing speed or tight tolerances. The Nail Machine from Gujarat Wire Products is a high-speed, precision-engineered machine designed for efficient nail production. It is built with durable components to ensure smooth operation and long-term reliability—demolishing that myth through cam-driven systems that maintain 0.05 mm head diameter consistency at 450 nails per minute.
Here’s the technical breakthrough: synchronized wire feeding with pneumatic cutting eliminates the micro-vibrations that plague standard machines. While competitors battle quality issues at high speeds, precision-engineered systems maintain pharmaceutical-grade consistency throughout production runs.
The Hidden Economics of Machine Selection
- Upfront Cost Blindness: Most buyers optimize for purchase price. Fatal error. A ₹2.5 lakh machine producing 200 nails/minute costs ₹0.42 per 1,000 nails in operator time. A ₹4.2 lakh machine at 400 nails/minute drops that to ₹0.21 per 1,000 nails.
- Maintenance Reality Check: Its product range includes pallet nails, construction nails, coil collated nails, and specialized fasteners. These offerings provide essential fastening solutions for wooden pallet assembly and construction projects, but unreliable machinery destroys profit margins faster than any competitor.
- The 18-Month Payback: Higher-capacity machines with robust construction typically recover their premium within 18 months through reduced downtime and higher throughput. Gujarat Wire Products is an ISO 9001:2008 company providing high-quality Nail Making Machine in India and worldwide—certification that matters when uptime determines profitability.
Market Timing: The Infrastructure Surge
India’s construction sector is experiencing unprecedented demand. Industries such as furniture, automobile, and electronics contribute significantly to the demand for wire nails, creating multi-sector opportunity beyond traditional construction applications.
- The Digitization Factor: Smart manufacturers now integrate IoT monitoring, predictive maintenance, and real-time quality control. Traditional suppliers offer machines. Modern suppliers offer production systems.
- Regional Advantage: Nail making is one of the profitable businesses, especially for manufacturers who understand that proximity to infrastructure projects reduces logistics costs while improving service response times.
Technical Specifications That Matter
- Wire Compatibility: Superior machines handle 2.5mm to 6mm wire diameter with automatic adjustment. No manual recalibration. No production stops.
- Production Flexibility: If you are familiar with the common iron nail, concrete steel nails, galvanized roofing nails, chipboard screw, wood screws, self-tapping screws, self-drilling screws, nuts, and bolts manufacturing industry, you know versatility drives profitability.
- Power Efficiency: Modern units consume 40% less electricity per 1,000 nails produced compared to decade-old designs. Environmental compliance meets cost reduction.
The Supplier Selection Framework
- Experience Depth: Gujarat Wire Products as a global leader in Wire Nail Making Machine and Wire Drawing Machine since 1975 represents nearly five decades of manufacturing evolution. New entrants lack the iterative refinement that creates reliable machinery.
- Service Infrastructure: Machine breakdown costs ₹8,000-12,000 per day in lost production. Suppliers with local service networks and spare parts availability prevent catastrophic downtime.
- Technical Support: Complex machinery requires skilled technicians. Choose suppliers who train your operators and provide ongoing technical consultation.
The Strategic Decision
The nail manufacturing landscape is polarizing. High-efficiency operators will capture expanding market share. Low-productivity players will face margin compression and market exit.
Profit of generic fastening products has been falling due to standardization, with increasing competition from low-cost, low-priced common iron wire nails from global manufacturers. The defensive strategy isn’t competing on price—it’s competing on speed, quality, and operational efficiency.
The Rajkot Advantage: Established manufacturers like Gujarat Wire Products combine decades of engineering refinement with modern production capabilities. Their machines don’t just make nails—they manufacture competitive advantage.